Imagine organizing a large event. One could try to do everything by oneself, from sending invitations to decorating the venue, and even preparing the food, while at the same time, a more viable and relaxed option is to simply hire an event management company to handle all the logistics from start to finish.
A fulfillment center works very much like the event company in the above illustration, as it offers businesses a comprehensive solution to manage inventory, packing, and shipping, saving the company from all the operational hassles.
Read on to discover more about the real meaning behind the fulfillment center, its key features, how it works, its advantages, and the essential factors to consider when selecting one.
Table of Contents
What is a fulfillment center
Key features of a fulfillment center
How a fulfillment center works
Understanding the benefits and selection of fulfillment centers
Efficiency delivered
What is a fulfillment center
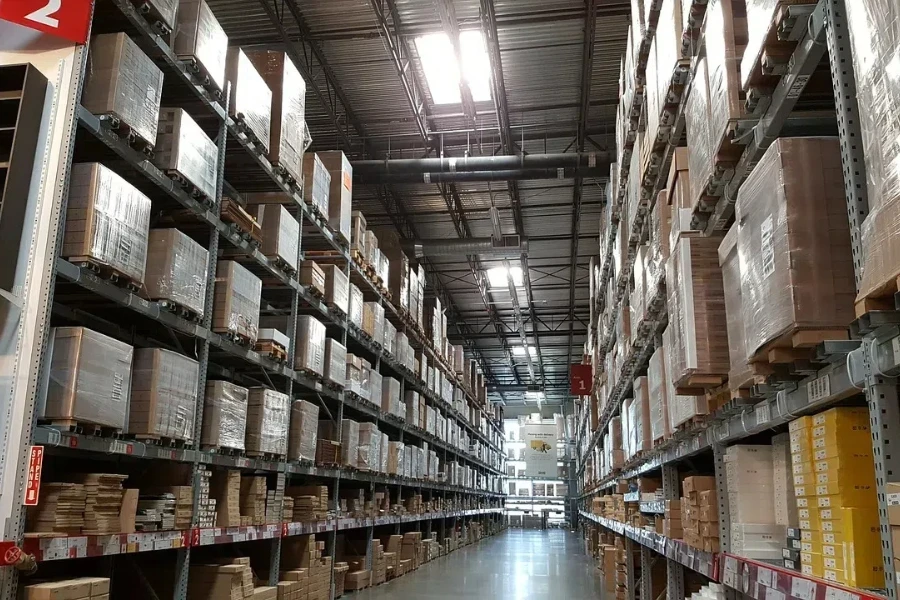
For a comprehensive grasp of what exactly a fulfillment center is, let’s look into several perspectives. From a logistical and functional outset, a fulfillment center (FC) is a crucial physical space or location within the supply chain network that acts as a hub to “fulfill”— which means to complete or satisfy customer orders by managing the entire order fulfillment process. This includes everything from inventory management and order processing to shipping, and, if necessary, also handling any return process.
Furthermore, for a more thorough insight into fulfillment centers, one can also explore their categorizations based on ownership and specialization. While most fulfillment centers are operated by third-party logistics providers (3PL), some larger companies run their own fulfillment centers to manage internal order requirements.
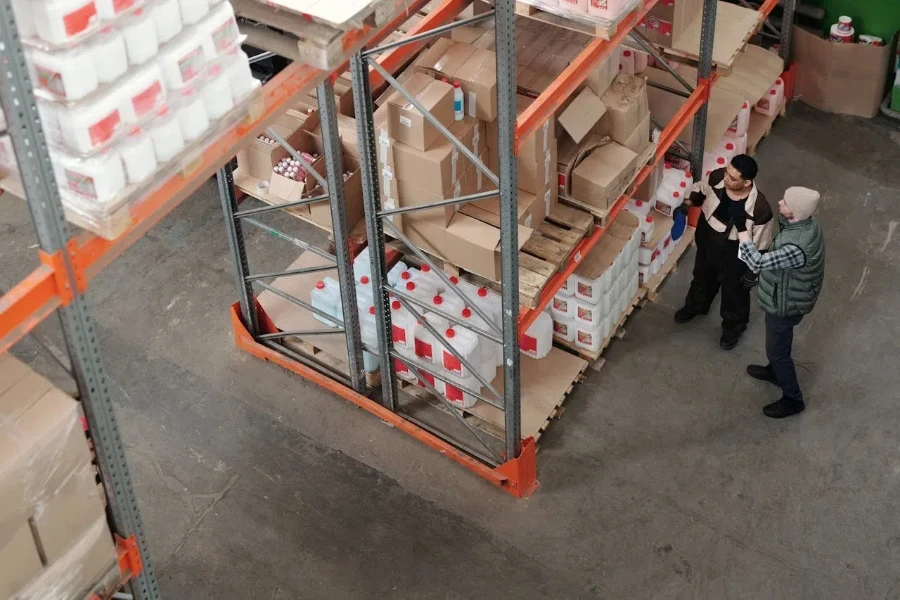
Regardless of whether a fulfillment center is owned by a 3PL or an internal division of a large company, they may focus on serving either ecommerce businesses or brick-and-mortar retail operations, or they can also concentrate exclusively on Business-to-Consumer (B2C) or Business-to-Business (B2B) transactions. Some advanced fulfillment centers may also operate in hybrid modes, taking up the role of both ecommerce fulfillment centers and retail store fulfillment companies and/or managing both B2C and B2B needs.
Aside from having expertise in ecommerce, being B2C/B2B focused, or even involved purely in reverse logistics management only, fulfillment centers are equipped with varying levels of technological sophistication. These tech-oriented features often include highly automated systems that streamline the manual fulfillment process or include specific tech-enhanced features. For example, a temperature-regulated fulfillment center is ideal for time-sensitive and temperature-dependent perishable goods.
Key features of a fulfillment center
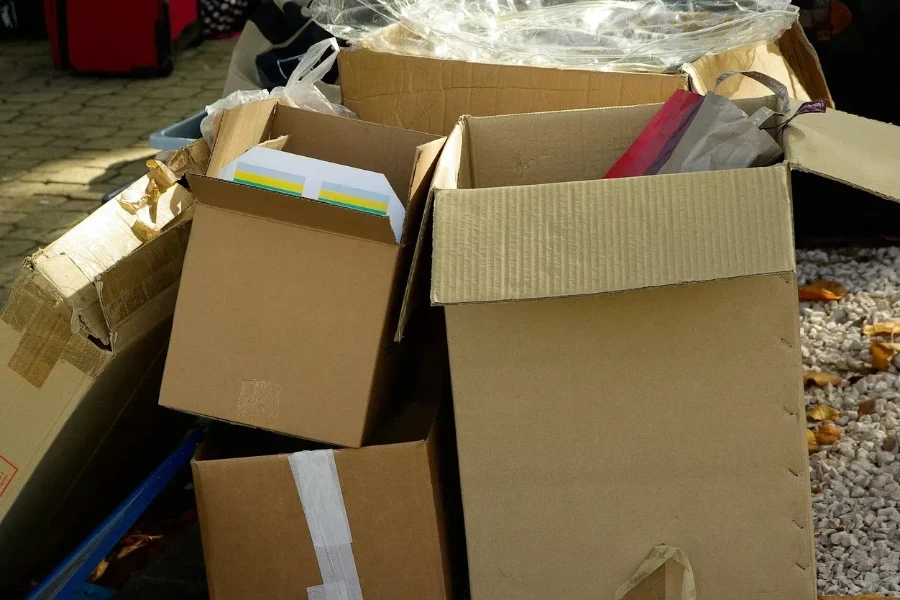
Since a fulfillment center plays the central role in executing the order from customers, it must be equipped with advanced inventory management and order handling systems to efficiently perform this task. Indeed, real-time tracking and control of inventory are among the most essential features that all fulfillment centers possess. Virtually all aspects of product storage, including stock levels in any relevant warehouse space as well as any part of the order management can be effectively monitored and controlled, via comprehensive inventory management systems within fulfillment centers.
Ultimately, the integrated inventory systems of fulfillment centers are designed to assist in facilitating the complete end-to-end order-handling process. That’s why besides inventory management, the fulfillment centers are also equipped with features that can manage and optimize the entire order workflow. From receiving goods from the supplier to picking, kitting, and packing them as required, to shipping them efficiently, the fulfillment center is capable of executing all such operations.
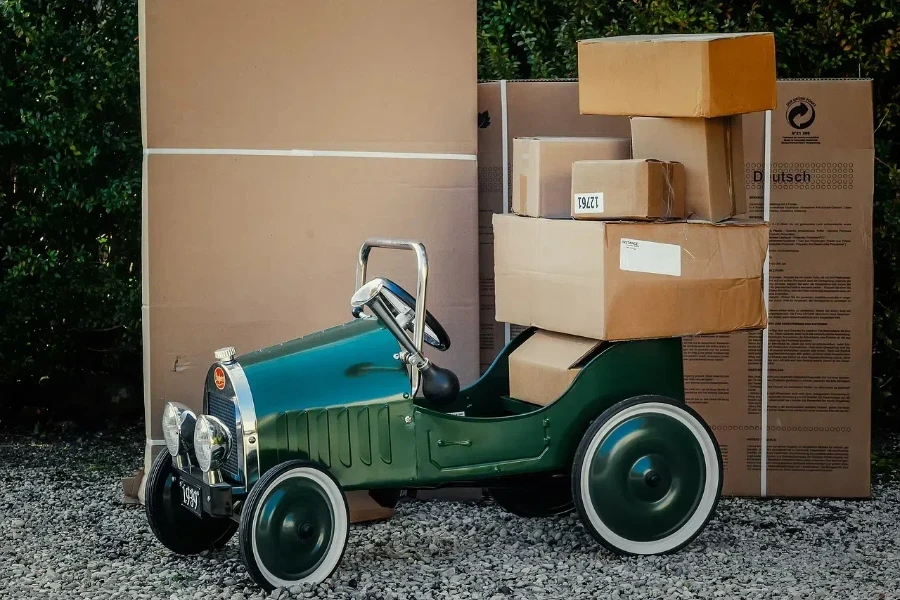
In the meantime, more advanced fulfillment centers also offer specialized handling and tailored storage options to accommodate unique product needs. Apart from that, enhanced transportation optimization strategies such as cross-docking help transfer products from incoming shipments to outgoing deliveries directly, minimizing storage time and improving inventory turnover levels.
Moreover, to improve efficiency for a more streamlined and comprehensive delivery and order processing service, some fulfillment centers also offer seamless integration of order processing across multiple sales channels. Lastly, most fulfillment centers also provide standard returns and reverse logistics management that helps handle returned items and manage the reintegration of products into the inventory.
How a fulfillment center works
Inventory reception and storage
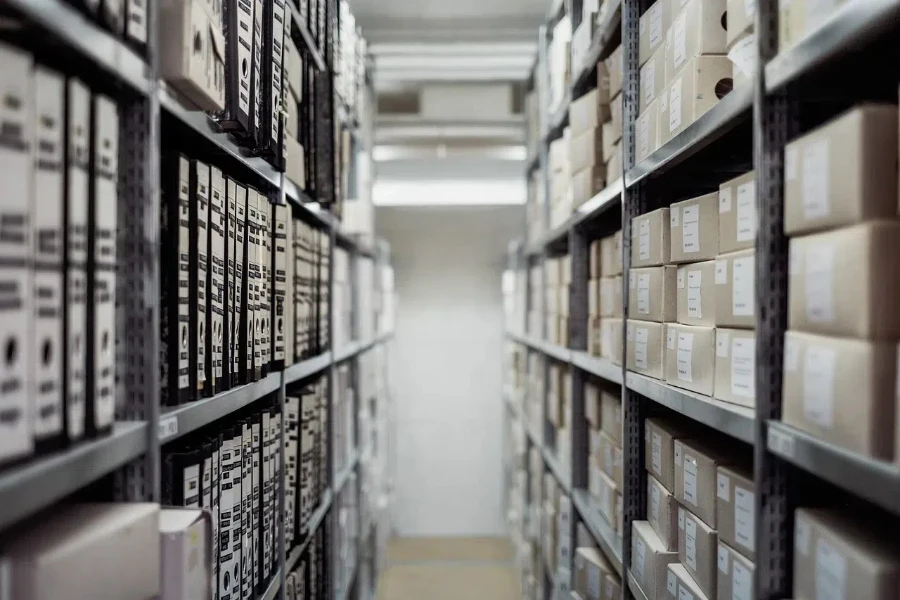
The initial steps in operating a fulfillment center often involve receiving and storing goods from the clients or suppliers, or manufacturers directly. The inventory reception process also covers inspection and quality checks to confirm that the products meet specified requirements before categorizing and storing them according to size, order frequency, and relevant picking or packing needs. This categorization is designed for quick and easy access to different types of goods when orders come in.
Order management and processing
Once the goods are received, inspected, and stored accordingly, the automated system of the fulfillment center should ensure automatic goods selection based on predefined criteria whenever there are any order confirmations. The goods will then be packed and labeled according to the order details, following necessary guidelines to protect the items with appropriate use of protective materials such as bubble wrap or customized packaging as required.
Shipping and distribution coordination
After the order is properly packed, the fulfillment center needs to coordinate with shipping carriers for prompt pickups and timely deliveries to customers. Advanced transportation strategies like cross-docking or specialized handling, including the inclusion of any marketing materials and custom labels, may be employed to minimize storage time and enhance overall delivery efficiency.
Returns and reverse logistics management
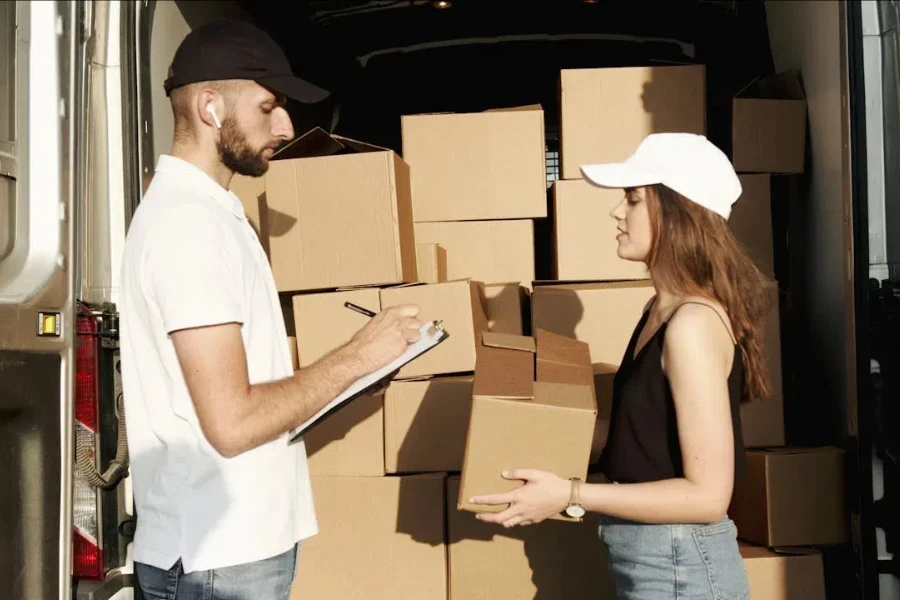
The responsibilities of some fulfillment centers do not end with the completed delivery but extend to efficiently receiving returned items, inspecting and restocking these items as necessary. During this process, the disposal or reintegration of the returned goods is also carefully managed to maintain operational efficiency and customer satisfaction.
Real-time inventory management and compliance
As part of the seamless operation of a fulfillment center, it’s worth noting that modern fulfillment centers must incorporate the latest technologies to ensure real-time inventory management and replenishment. The real-time system should assist in monitoring stock levels and tracking orders to mitigate any stockout risks and streamline operations.
Finally, throughout the entire fulfillment process, fulfillment centers must also ensure compliance with tax and legal requirements according to their specific roles or client needs. For example, for eCommerce operations, fulfillment centers must ensure compliance with dropshipping regulations, whereas, for B2B transactions, they have to adhere to legal obligations for cases involving consignment sales.
Understanding the benefits and selection of fulfillment centers
Benefits of using fulfillment centers
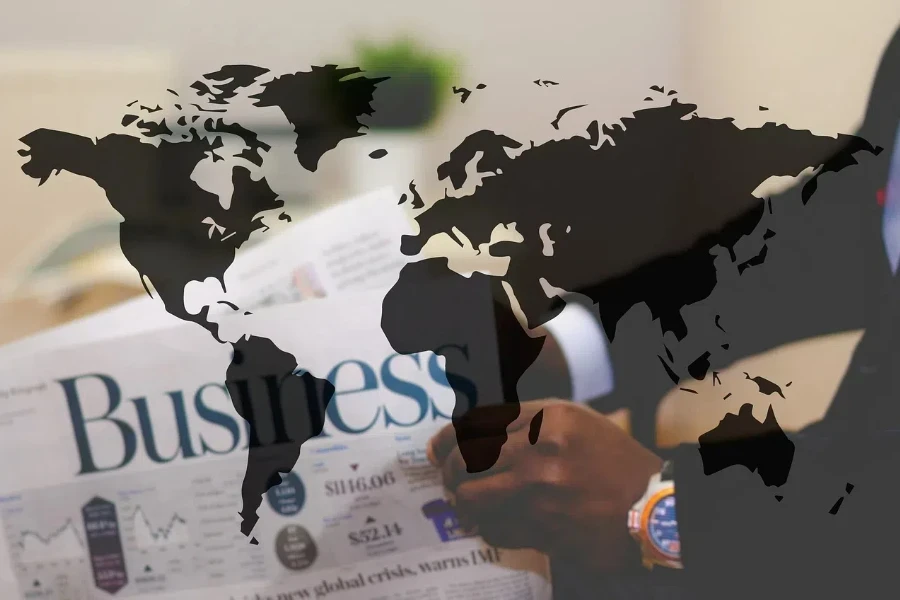
While both company-owned and 3PL-owned fulfillment centers each offer unique benefits to their clients, there are several common advantages that are shared by these two types of fulfillment centers.
First of all, rather than handling the often tedious and complex logistical tasks, a fulfillment center helps business owners shift their focus to core business activities and strategic growth instead. For businesses that outsource order fulfillment to a 3PL, this benefit becomes even more prominent. Essentially, these businesses gain more time and resources through outsourcing as their inventory management becomes much simpler and less demanding. Moreover, they also sidestep the need for significant investments in technology equipment, software, and systems upgrades which would otherwise almost certainly incur substantial costs.
On top of these common benefits, fulfillment centers help achieve cost savings in several ways: optimizing operations and leveraging economies of scale in shipping to negotiate for better rates with carriers. To be precise, businesses that rely on 3PL-owned fulfillment centers experience even greater savings from reduced manpower needs and the elimination of physical infrastructure requirements. Even better, these savings can then be redirected toward enhancing marketing, customer service, and all other areas that help to improve the overall customer experience.
Meanwhile, beyond these key benefits shared by both types of fulfillment centers, there are two other significant advantages specific to outsourced fulfillment centers: scalability and strategic location. Fundamentally, since these businesses save on the costs of establishing and operating their own fulfillment centers, they can be more adaptable to scalable solutions that can adjust to varying business needs—whether it’s a peak season, off-peak period, or a temporary spike in demand due to promotions.
These are further reinforced with the strategic fulfillment center locations which are situated near major customer bases or shipping hubs. These strategically placed centers significantly enhance the market reach of businesses that opt for 3PL fulfillment centers, as their last-mile deliveries can now be completed in a quicker and more efficient way, which in turn helps to improve customer expectations and enhance the overall delivery experience.
Key factors in choosing a fulfillment center
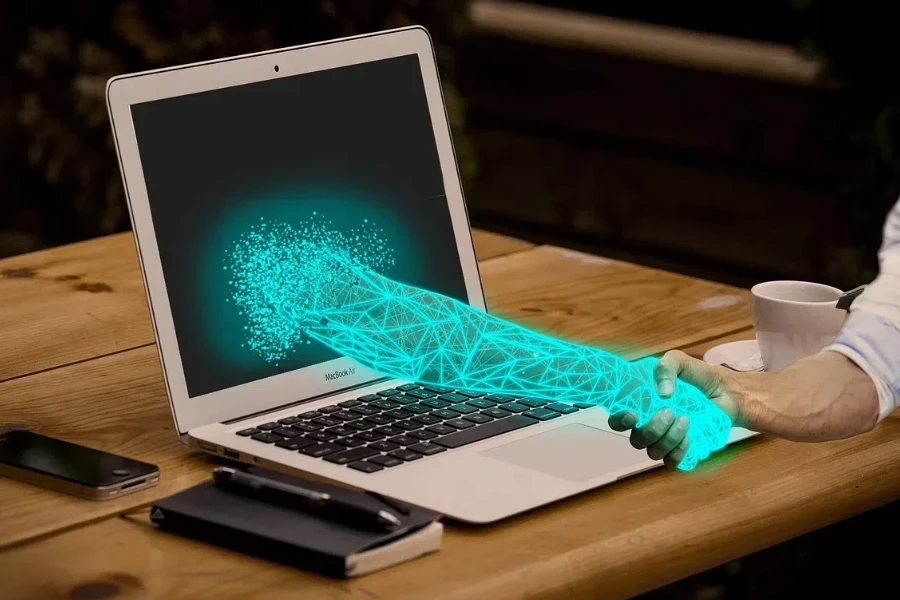
Apart from some large enterprises or specialized businesses that find it more cost-effective to operate their own fulfillment centers, the majority of businesses opt for 3PL-run fulfillment centers due to the various flexibilities and efficiencies they offer. In line with such a growing trend, it is crucial to evaluate the key factors in selecting the right fulfillment center.
While there are several important factors to consider when choosing a 3PL-owned fulfillment center, the availability of a broad network of strategically located centers is certainly among the top priorities. This is because the close proximity of these centers to major customer bases often translates to lower shipping rates and faster delivery times, both of which are essential for attracting customers.
Furthermore, the technological sophistication and automation capabilities of a fulfillment center are two other critical factors that businesses must evaluate. Essentially, regardless of how advanced or how automated the operations of a fulfillment center may be, it is vital for businesses to ensure that they are fully compatible with their existing inventory management and related software for a seamless, real-time integration. Lastly, it is equally important to assess the consistency and quality of service across all fulfillment centers with a wide geographical presence to maintain reliable delivery and consistent customer satisfaction.
Efficiency delivered
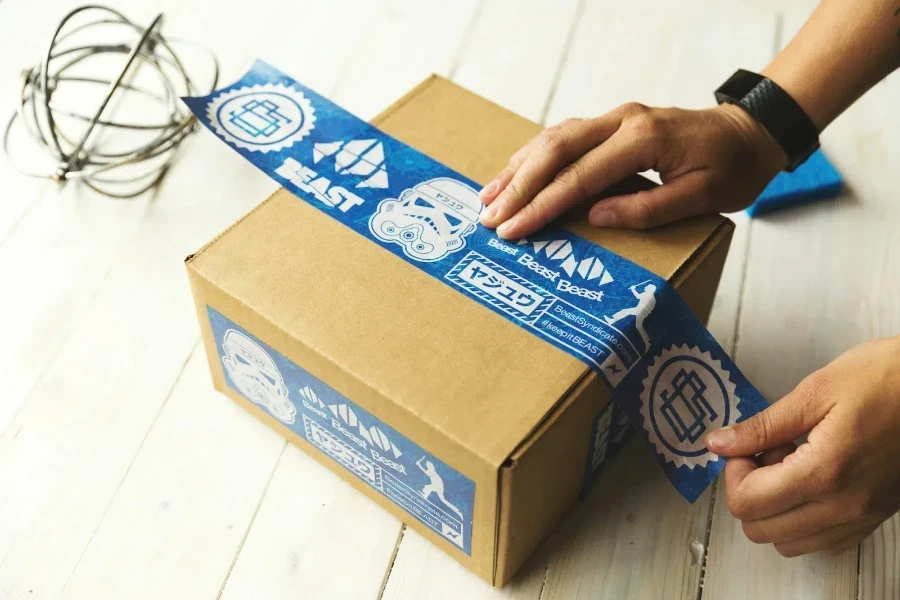
From inventory reception and storage to order management, processing, shipping, and returns logistics management, fulfillment centers are equipped with sophisticated software and systems that provide real-time order tracking and delivery status updates to ensure a smooth and efficient order fulfillment process.
In a nutshell, fulfillment centers help businesses streamline their order fulfillment process, achieving cost savings through more efficient operations and also by tapping on high-volume operations to obtain reduced shipping rates from carriers. Companies using 3PL-owned fulfillment centers, in particular, can benefit from significant savings as they bypass the need for additional staff and investments in physical infrastructure. Moreover, these businesses can also capitalize on the strategic locations of 3PL centers to expand their market reach.
By considering the strategic locations of fulfillment centers, their consistent service performance across different locations, and the compatibility of relevant systems that can be seamlessly integrated into existing operations, businesses can make informed decisions when selecting the fulfillment centers best suited to their needs.
For expert logistics insights, updates, and knowledge, visit Chovm.com Reads regularly. Discover wholesale business ideas, the latest sourcing market trends, and innovative strategies that drive business success and growth from here.